Non – Contact 80 GHz level sensors in the Juice Industry
As far as the eye can see there are fruit trees surrounding the production site, so the first step is to harvest the fresh fruit. The apples and oranges then get delivered by lorries to the production site where they get put into a floating tank. From there on the fruits get moved to a polisher.
Afterwards the raw material gets transported by water to the mills which chop the fruits and then the raw material gets compressed into tubes.
Finally the Juice gets transferred to a process room where further ingredients get added. Before they get transmitted to the cooled final tank room, the juices get transported to the mix tanks where they get mixed with other juices in order to create new flavors.
The site is not only producing and storing the juice, but they also produce their own bottles. Therefore they have plastic blanks which they put into special moulds. As soon as the blank is put into the mould the plastic gets heated up and high air pressure gets blown into the blank. As a result it extends and adapts to the shape of the mould.
After the bottles got produced they get transported to a cleaning machinery where they are sterilised so they are ready to be filled. The juice is stored in the buffer tank until ready.
Next the filled bottles get heated up and shortly after that they get cooled down again. This process has the aim to kill any kind of bacteria which might be contained in the juice.
Therefore VEGA Controls Ltd. sent their Service Manager Kevan Rocliffe and Senior Sales Engineer Matthew Westgate to the production site of Konings in Sudbury.
At first they installed the VEGAPULS 64 by placing the device on the top of the vessel and setting up the customized parameters.
In order to check the function of the VEGA probe they filled up the vessel with water and inspect the development of the echo curve. The curve showed that not only the water but also the metal vessel itself, reflecting the radar pulses sent out by the VEGAPULS 64. But as the reflected pulses of the vessel had a lower energy content than those by the water the VEGAPULS 64 indicated the correct vessel level.
As the customer is going to store beverages in the vessel there are high hygienic standards which have to be taken into account when installing the probe.
After each filling process the vessel needs to be cleaned. This cleaning process is done with the help of a spray ball. This spray ball gets placed in the empty tank and connected to the water. The spray ball then sprays a mixture of water and detergent in a radius of 360 degrees within the vessel.
The task of the VEGAPULS 64 during this cleaning process is to make sure that the vessel will not over flow. Due to the water which gets sprayed the VEGAPULS 64 detects interfering signals.
Therefore the Service Manager of VEGA Controls had to make sure that those signals don’t effect the correct level display.
All those tests showed that the VEGAPULS 64 was not affected by those conditions in his function.
As mentioned before there is a high hygienic standard in the food and beverage industry. Therefore the juice company has to make sure that the VEGAPULS 64 will not cause any problems regarding bacteria. As a result of that the employees of Konings put apple juice on the device’s lens. Then they put the device back on the top of the vessel and started the cleaning process.
After the cleaning process was finished they took the probe from the vessel and put it into quarantine. After two weeks in isolation the employees of Konings will check if there has been growth of any kind of bacteria.
If no bacteria has developed then the VEGAPULS 64 will be installed permanently at Konings Juice & Drinks UK Ltd.
Industry
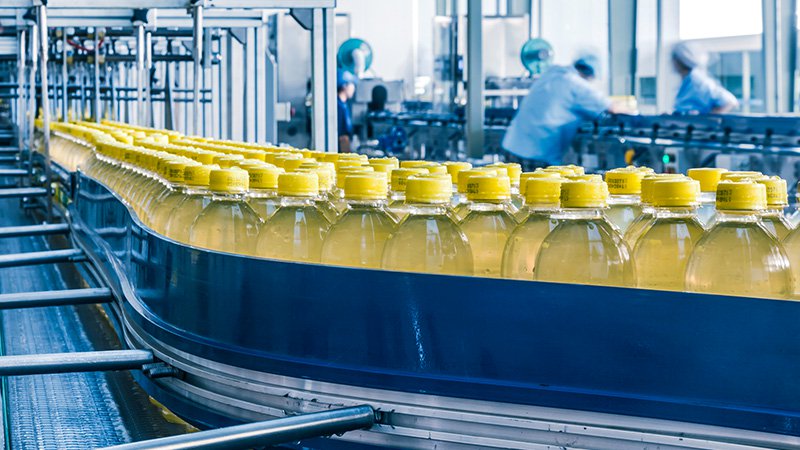
Food industry
Products
Export this article
Download as PDFShare this article
Comments ({{comments.length}})
{{getCommentAuthor(comment, "Anonymous")}} {{comment.timestamp | date : "dd.MM.yyyy HH:mm" }}
{{comment.comment}}