VEGA-Sensoren mächtig unter Druck
Der TDR-Sensor VEGAFLEX 86 meistert erfolgreich die herausfordernde Messsituation im Kernkraftwerk in China.
Das Gasabscheidesystem gilt als Schlüsselsystem zwischen der Hoch- und der Niederdruckturbine eines Kernkraftwerks in China, das über eine Leistung von 1000 MW verfügt. Der Dampf von der Hochdruckturbine weist 14 % Feuchtigkeit auf, so dass dieser, bevor der Dampf in die Niederdruckturbine geleitet wird, zunächst entfeuchtet wird. Anschließend wird dieser Dampf erneut erhitzt. Das Kondensat wird gesammelt und in Behältern, die mit einem Ablauf versehen sind, aufbereitet. Die Kondensatbehälter spielen eine wichtige Rolle im Gasabscheidesystem. Das Wasser im Abwassertank darf einen bestimmten Füllstand nicht überschreiten. Denn: Ist der Tank zu voll, besteht die Gefahr, dass das Wasser in das Gasabscheidesystem gelangt, dadurch erhöht sich wiederum die Feuchtigkeit des Dampfes, wodurch dann die Niederdruckturbine beschädigt werden kann. Damit übernimmt die dort installierte Füllstandmessung eine wichtige Aufgabe für den sicheren und effizienten Betrieb des Gasabscheidesystems sowie der Turbinen.
Dabei geht es in den kugelförmigen Tanks mit einem Durchmesser von 2 m hoch her:
- die Prozesstemperatur liegt bei 280 ℃
- der Druck bei 66 bar
- bisherige Füllstandmesstechnik: Geführte Radarmessgeräte eines anderen Herstellers
- drei Messgeräte pro Behälter, die in einer 2 aus 3-Auswahlschaltung arbeiten
Hierbei wurde der durchschnittliche Füllstand der drei Messungen vom System als Niveau des Behälters festgelegt. Die drei Messgeräte waren direkt im Behälter statt in Bypassrohren installiert.
Anwendungen
Kondensatbehälter
Füllstandmessung und Grenzstanderfassung in Kondensatbehältern
In den verschiedenen Prozessanlagen wird sauberes, wiederverwendbares Kondensat in Behältern gesammelt. Dieses Kondensat entsteht im Dampfsystem, mit dem die verschiedenen Kohlenwasserstoffprozesse erhitzt werden. In den Kondensatbehältern herrschen gewöhnlich hohe Prozesstemperaturen, so dass eine für diese Prozessbedingungen geeignete Füllstandmessung und Grenzstanderfassung erforderlich sind.
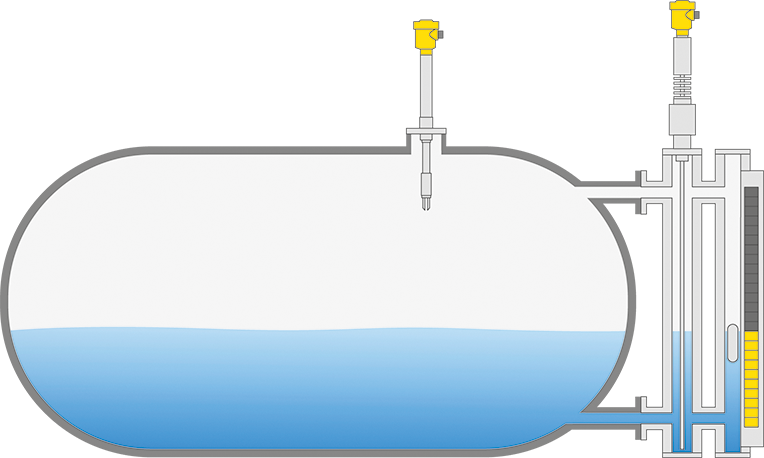
Sicher
Sichere Messung unbeeinflusst durch hohe Temperatur und Dampf
Wirtschaftlich
Wartungsfrei durch optimale Redundanzanordnung
Komfortabel
Einfache Inbetriebnahme und Installation
Sensoren müssen hohen Druck und hohe Prozesstemperatur aushalten
Insbesondere der hohe Druck des Dampfes führte zu einigen Schwierigkeiten. Bereits kleinste Wassertropfen können bei hohen Geschwindigkeiten eine enorme Kraft entwickeln und viele Werkstoffe angreifen. Auch in dieser Anwendung verursachte der Dampf immer wieder Probleme an mehreren Stellen.
❗ Schwachpunkt Nummer 1: die Abstandshalter
Diese sind nötig, da ansonsten bei jeder Vibration oder einem mechanischen Stoß die Stabsonde das Koaxialrohr berühren und wiederum zu Messwertsprüngen führen würde. Diese Abstandshalter bestanden aus PEEK und wurden durch den heißen Dampf immer wieder angegriffen, spröde und zerbrachen schließlich. Dabei besteht immer die Gefahr, dass Teile der Abstandshalter in das Dampfsystem eindringen und den sicheren Betrieb der Turbine gefährden. Man behalf sich, in dem die Koaxialsonde jedes Mal mit der Wartung der Turbine ausgetauscht wurde.
❗ Schwachpunkt Nummer 2: die Abdichtung zum Gerät
Der Dampf durchdrang das Dichtungssystem und trat in das Gehäuse ein. Dadurch wurde das Messgerät immer wieder beschädigt. Im Nachhinein stellte sich heraus, dass die O-Ring-Dichtung des Gerätes nur Temperaturen bis 150 ℃ standhalten konnte und auch beim Isoliermaterial PEEK die Temperaturgrenze bei 250 ℃ lag. Beide Temperaturgrenzen waren also deutlich niedriger als die der Prozesstemperatur von 280 ℃.
Die Dielektrizitätszahl ändert sich je nach Druck und Temperatur. Dampf hat eine höhere Dielektrizitätszahl als Luft. Dies hat zur Folge, dass die Ausbreitungsgeschwindigkeit von Mikrowellen im Dampf abnimmt. Das Messgerät gibt dadurch einen niedrigeren Füllstand an als tatsächlich vorhanden. Diese Messabweichung wurde zwar kompensiert, aber nur unzureichend.
Die Messabweichung der drei Feldgeräte bei Prozessbeginn betrug immer weniger als 20 mm, dies galt allerdings nur im abgekühlten Status. Sobald das Turbinensystem aktiviert wurde und die Prozesstemperatur und der Druck im Kondensatbehälter stiegen, wurden auch die Messabweichungen allmählich größer und lagen durchaus bei bis zu 100 mm oder mehr. Auch hier behalf man sich über viele Jahre mit einer Notlösung, indem man den gemessenen Wert jedes Mal korrigierte, sobald die Abweichung zu groß wurde.
Geführter Radarsensor VEGAFLEX als Problemlöser
Für die Betreiber war dies unbefriedigend und man machte sich auf die Suche nach einer anderen Lösung.
👍 Fündig wurde man bei VEGA und dem VEGAFLEX 86 mit Dampfkompensation. Dieser robuste Sensor zur kontinuierlichen Füllstand- und Trennschichtmessung von Flüssigkeiten hat sich vor allem unter extremen Temperatur- und Druckbedingungen durchgesetzt. Das Gerät verfügt über eine Keramikisolierung und Graphitdichtung in der Einkopplung verfügt, welche dem Eindringen von Dampf mit einem Druck von max. 400 bar und einer Temperatur von 450 °C standhalten können.
Auch für die sich ändernde Dielektrizitätszahl wurde bei diesem Geführten Radarsensor eine gute Lösung entwickelt. Eine innovative Dampfkompensation bringt eine höhere Messgenauigkeit mit sich. Der VEGAFLEX 86 verwendet eine Referenzstrecke, um die durch Hochdruckdampf verursachte Abweichung zu kompensieren. Je länger diese Strecke, desto genauer die Messung. Der VEGAFLEX 86 verfügt über die längste Referenzstrecke am Markt. Wir benötigen Ihre ZustimmungDieser Inhalt wird von einem externen Anbieter bereitgestellt. Wenn Sie den Inhalt aktivieren, werden ggfs. personenbezogene Daten verarbeitet und Cookies gesetzt.
Verwandte Branchen

Refining und Petrochemie
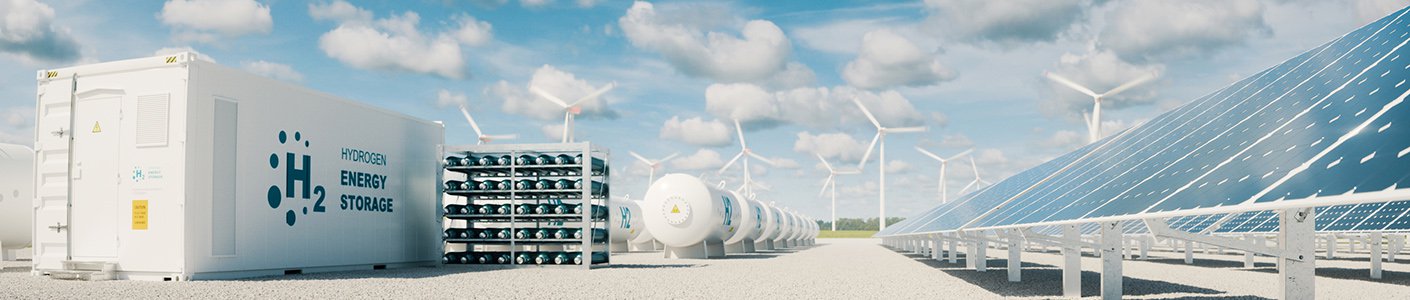
Energie
Produkte
Ähnliche Beiträge
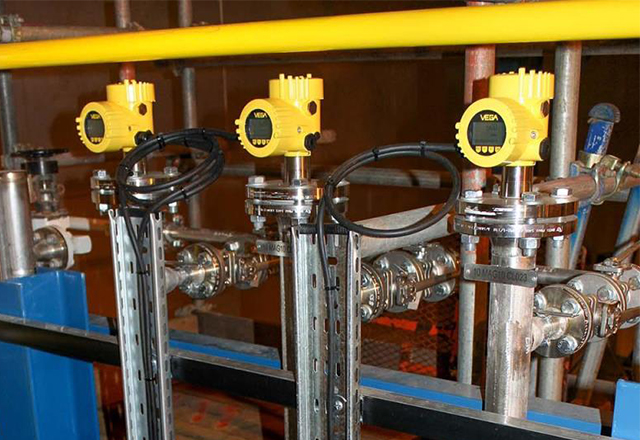
Kraftwerk im Gleichgewicht mit VEGAFLEX 81
weiterlesen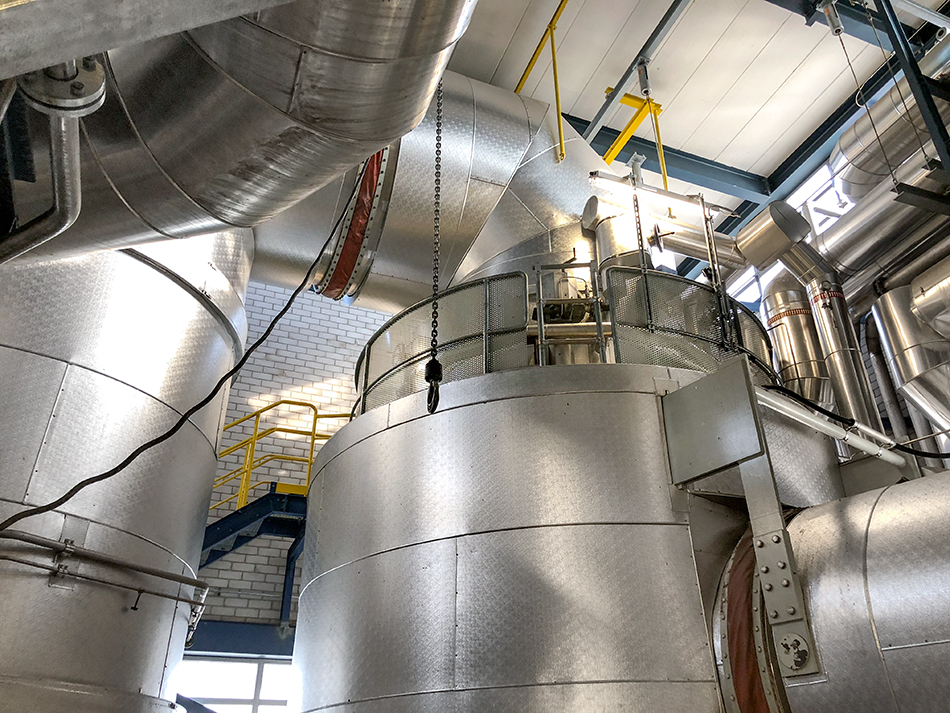
Geführter Radarsensor VEGAFLEX macht Dampf für die effiziente Prozesswärmeversorgung
weiterlesenDiesen Artikel exportieren
Als PDF herunterladenBeitrag teilen
Kommentare ({{comments.length}})
{{getCommentAuthor(comment, "Anonym")}} {{comment.timestamp | date : "dd.MM.yyyy HH:mm" }}
{{comment.comment}}