Finding the optimum level in coke drums: Application of the month
The delayed coking unit is a refining process that uses heat to crack heavy residuum crude oil residual into lighter, more useful hydrocarbons. The refinery is boiling oil in the coke drums to capture released hydrocarbons in the vapor overhead nozzle above and transporting them to the next step in the process, the fractionator. This entire process is a lengthy one, and to maximize efficiency, refineries most commonly operate coke drums in pairs – as one is getting filled, the other gets cleaned out.
Operationally, refiners look to fill the coke drum with as much hydrocarbon as possible while maintaining safe practices. If the drum is filled too low, revenue is lost due to inefficiencies, and if filled too high, particulates or antifoam can reach the vapor overhead nozzle, causing blockages or damaging equipment downstream. This is a critical refinery processing unit where operators are constantly trying to maximize efficiency, and it takes a reliable level measurement to fill the coke drum accurately.
Coke drums
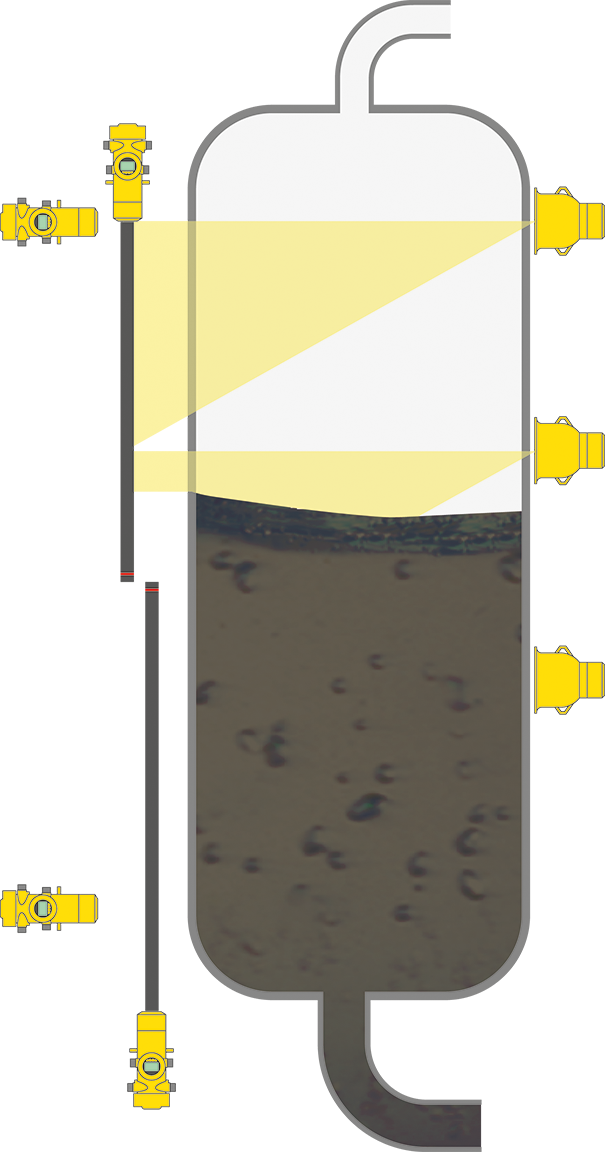
Density, level measurement and point level detection in coke drums
To the applicationFractionator
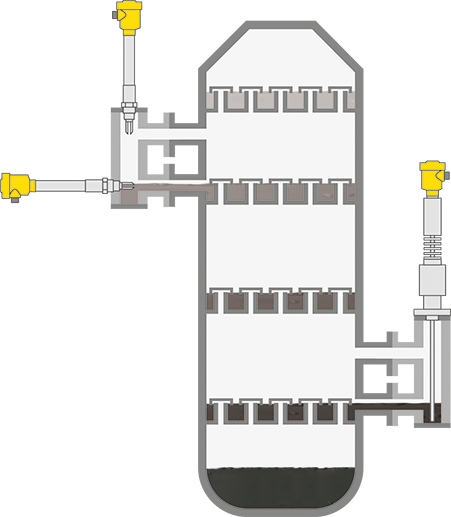
Level measurement and point level detection in the fractionator
To the applicationMonitoring level and maximizing throughput
On the outside, coke drums are large dimeter vessels, often with thick walls. And on the inside, it’s a hot, sticky, violent environment. These factors make it exceptionally difficult for operators to measure level using traditional measurement instrumentation. Radiometric sensors are a refinery’s best option because these instruments are completely external and immune to thermal expansion and aggressive process conditions.
VEGA’s coke drum continuous level solution has evolved since it was first introduced. VEGA recommends tracking continuous level throughout the top half to one-third of the vessel while monitoring the top of the vessel for any unwanted particulate matter that may escape through the vapor overhead nozzle. In addition, VEGA recommends using a point switch at the bottom of the level system to ensure a good zero starting point between cycles.
VEGA uses the FIBERTRAC 31, a MINITRAC 31, and a POINTRAC 31 to give operators a full picture of what’s happening inside the delayed coking units. The FIBERTRAC 31 allows operators to monitor the level as the coke drum fills, giving them more control over the filling process and providing a better idea when to add antifoam agent. The MINITRAC 31, placed on the top of the vessel, operates as a vapor compensation gauge, which will begin to spike near the end of the fill cycle as particulate matter begins to carry over more due to the overall level in the drum. And the POINTRAC 31, placed near the bottom of the vessel, is the auto-zero gauge, which zeroes the entire system after the coke drum has been emptied and cleaned. This provides more accurate measurements to operators cycle after cycle.
Reliable, accurate measurements well into the future
Using multiple sensors on a single application gives operators more control in arguably the most important application at any refinery. Continuous level sensors, a vapor compensation gauge, and an auto-zero gauge all work together to provide the full picture of what’s happening inside the coke drum. Radiometric technology can make all of these measurements without ever interfering with the process because everything is external. And because they’re not touching any of these volatile processes, the durable instruments can last longer with little to no maintenance.
Related products
Export this article
Download as PDFShare this article
Comments ({{comments.length}})
{{getCommentAuthor(comment, "Anonymous")}} {{comment.timestamp | date : "dd.MM.yyyy HH:mm" }}
{{comment.comment}}