VEGA Pressure Measurement Technology for the Production of Decor Paper
Decor papers are special papers for the surface finishing of wood-based materials for furniture, floors or wall panels. Since the optical quality of the end product is decisive here, very high demands are placed on them. In the production of decor paper, sensors are particularly vulnerable to wear and tear due to abrasive fillers such as titanium dioxide as well as to in-line, high-pressure cleaning of the pipelines. In the case of pressure transmitters, this often results in high failure rates and a service life of only a few weeks. Every sensor exchange also involves a costly pre-calibration of the instrument in the installation position in the workshop as well as frequent recalibration after installation. That’s why maintenance planners decided very early on to use pressure transmitters with ceramic measuring cells from VEGA.
Since then, VEGA’s precise, overload resistant pressure transmitters have been ensuring the integrity of all decisive production steps on PM 15 – from the dye mixing system to the headbox, and from the dryer section to the calendar.
Unique features of VEGA pressure transmitters with ceramic measuring cells
At the headbox, a fibre suspension is sprayed onto the wire screen. The jet velocity of this suspension is decisive for the strength of the paper in both the lengthwise and crosswise direction. It should be identical to the wire speed, but via small intentional variations it can set the longitudinal/transverse ratio. The VEGABAR 82 flush-mounted pressure transmitters installed at the headbox on the operator side and drive side allow the dynamic pressure to be precisely measured. Possible pressure differences between the two sides are detected and can be compensated by the return flow of the cross-flow distributor.
This is where the special features of this pressure transmitter come into play: very high measurement accuracy (measuring error < 0.05% !), absolutely flush installation in the side wall of the headbox, and space-saving design in protection class IP 68 (25 bar).
Summary
Related applications
Drying-cylinder
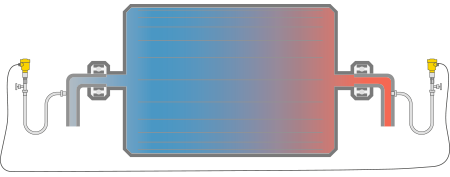
Differential pressure measurement in the drying cylinder
To the applicationHeadbox
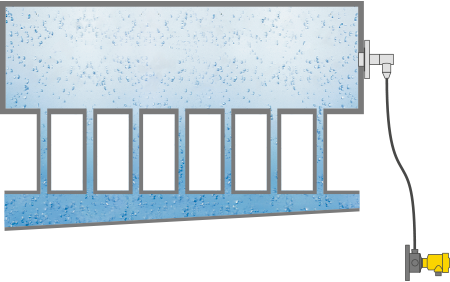
Pressure measurement in the headbox
To the applicationDrying-cylinder
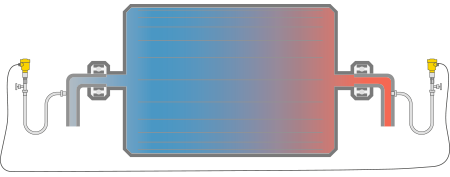
Differential pressure measurement in the drying cylinder
To the applicationWe need your consent
This content is provided by an external provider. If you activate the content, personal data may be processed and cookies set.
Export this article
Download as PDFShare this article
Comments ({{comments.length}})
{{getCommentAuthor(comment, "Anonymous")}} {{comment.timestamp | date : "dd.MM.yyyy HH:mm" }}
{{comment.comment}}