Stock preparation for cartonboard machine modernised with VEGABAR sensor technology
The LEIPA GROUP is an independent family business – for over 170 years it has stood for environmentally friendly processes and technologies in the area of paper and packaging based on 100% recycling. The range of business activities in Schrobenhausen, where the company was founded, include the cartonboard and specialty paper segments as well as the LEIPA FlexPack business unit. The latter offers paper-based solutions in the area of flexible packaging.
LEIPA multi-ply grey carton board is, so to speak, the "classic product" for secure protection of valuable products in boxes and packagings. But it is also a popular standard solution for pallet covers or hardbound books. The environmentally friendly material with grammages ranging from 300 to an impressive 950 g/m² is extremely resistant and stable and is used in a wide range of applications.
Especially in recovered paper processing, the deployed measurement technology is subject to extreme mechanical stresses caused by abrasive residues in the suspension or the vibration of refiners or standpipes of MC pumps, as well as hydraulic shock resulting from quickly closing valves. Further challenges for every measuring system are: varying stock densities as well as agitators in vats and stock towers. The internal cleaning of equipment components with aggressive chemicals and external cleaning with high pressure cleaners are additional factors that have to be reckoned with.
Sensors have to measure precisely and reliably in spite of these challenging conditions. VEGA understood the advantages of robust ceramic early on and came up with a sophisticated sensor design utilising the dry, capacitive measuring cell CERTEC®. High-purity alumina ceramic (99.9% Al2O3), which is second in hardness only to diamond, is used as the diaphragm material. This protects against abrasion, especially in cleaners, and ensures the long service life required for profitable continuous operation.
We need your consent
This content is provided by an external provider. If you activate the content, personal data may be processed and cookies set.
Industry
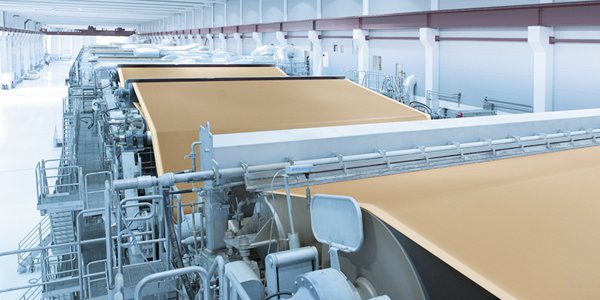
Paper industry
Products
Export this article
Download as PDFShare this article
Comments ({{comments.length}})
{{getCommentAuthor(comment, "Anonymous")}} {{comment.timestamp | date : "dd.MM.yyyy HH:mm" }}
{{comment.comment}}