Optimizing feed water systems in energy production with guided wave radar technology
VEGA's expertise in action
VEGAFLEX 86 sensors were chosen for their advanced GWR technology, offering exceptional accuracy in high-temperature environments. These sensors are installed in the feed water system across various stages, including Low Pressure Heaters (LPH) 1, 2, 3 and High-Pressure Heaters (HPH) 5, 6, and 7. The process they monitor is characterized by a demanding environment with temperatures around 170 degrees Celsius and pressures reaching 21 bar for LPH and 350°C / 80 bar for HPH. Despite these challenging conditions, VEGAFLEX 86 sensors demonstrate outstanding performance, providing reliable measurements crucial for controlling water levels and maximizing the output temperature of the feed water heater. The integration of VEGA sensors into the system was a collaborative effort between the PT KPJB team and VEGA engineers. The setup process was smooth, with the sensors proving to be user-friendly and easy to configure. This partnership not only ensured a seamless installation but also provided valuable insights into optimizing sensor performance for specific needs.
Overcoming the challenges
The production site, while very clean, is surrounded by the constant noise typical of a large-scale power plant. The environment poses further challenges, such as high temperatures, the presence of steam, and the need for precise measuring water level with high temperature steam. VEGAFLEX 86 sensors excel in this setting due to their robustness and high accuracy. Their ability to consistently deliver precise readings, unaffected by water vapor, could significantly improve the reliability of the feed water system.
Prior to the adoption of VEGA sensors, the process faced several issues. The differential pressure measurement system used was unable to determine the exact position of the water surface due to the presence of steam and density changed, leading to frequent hunting and instability. This not only affected the efficiency of operations but also increased maintenance requirements and costs. Since the installation of VEGAFLEX 86 sensors in February 2021, there has been a marked improvement in the accuracy and reliability of measurements, translating into more stable and efficient operations.
A well-known name in the industry
VEGA was recommended to the technicians at PT KPJB by experienced industry experts and has not disappointed the high expectations placed in it. Since commissioning, the measuring instruments have impressed with their reliability and user-friendliness. The active support provided by VEGA engineers during set-up and the subsequent ongoing support have further strengthened confidence in the chosen solution with VEGA sensors.
A trusted partner
For PT KPJB, the joint journey with VEGA began in February 2021. Even in this short time, the company has proven to be an indispensable partner with the right goals. VEGA stands out not only for the quality of their sensors but also for their commitment to customer support and continuous improvement. Their products are designed with the end-user in mind, offering features that simplify installation and configuration while delivering unmatched performance. As proof of its satisfaction with VEGA, PT KPJB recommends the sensors to others. The VEGAFLEX 86 sensors have not only met but exceeded expectations and have become an important part of the feed water system.
Kamil Faishal, Assistant Junior Engineer Control and Instrument Maintenance staff at PT KPJB, played a key role in the success of the partnership project. When integrating the VEGA sensors into the feedwater system, Faisal worked closely with the VEGA engineers to ensure a seamless transition. His hands-on approach and attention to detail ensured that the sensors were configured to meet the specific requirements of PT KPJB's operations.
Success through reliability
In the ever-evolving landscape of power generation, long-term partners like VEGA are particularly important. Their sensors are important companions as they provide the precision and reliability required to supply customers with high-quality products. PT KPJB will continue to rely on the best available technology in the future, and VEGA has established a position to once again play a key role.
Condensate, buildup and foam are present in many processes. Even under these conditions the guided radar sensors of the VEGAFLEX 80 series enable safe and reliable level measurement.
We need your consentThis content is provided by an external provider. If you activate the content, personal data may be processed and cookies set.Related industries

Coal power plant
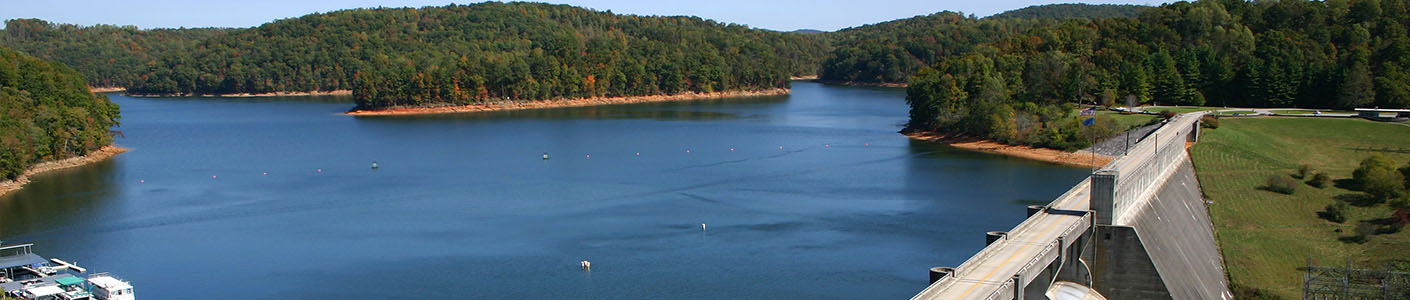
Hydropower
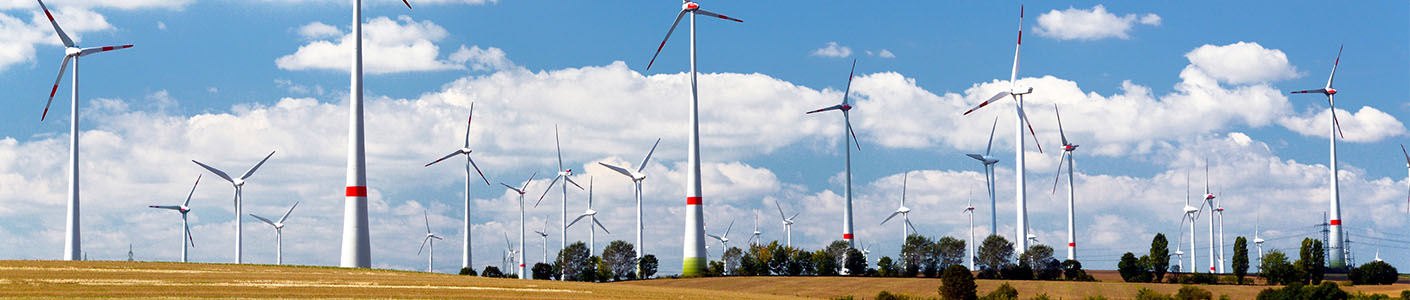
Wind power
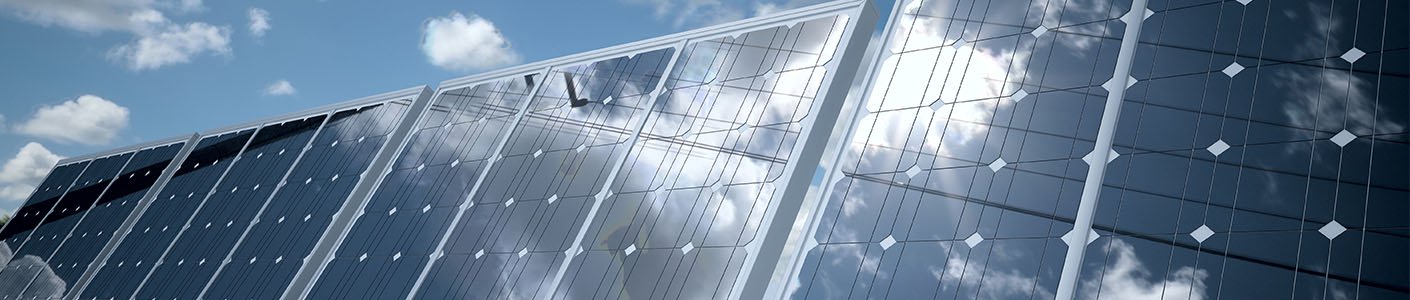
Solar energy
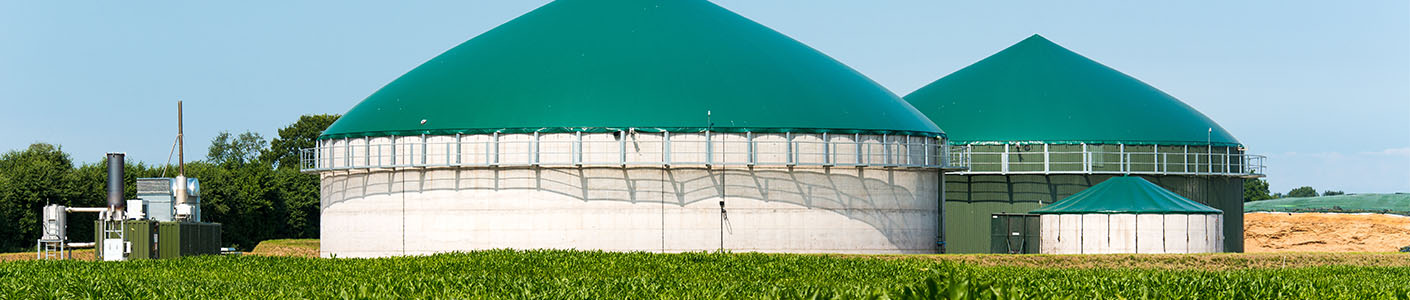
Biogas
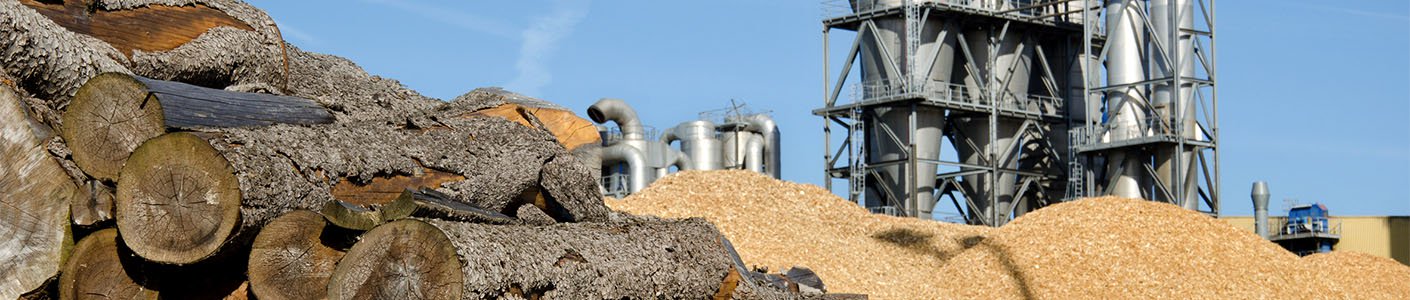
Products
What is SIL?
SIL stands for Safety Integrity Level: But it is also sometimes referred to as Safety Requirement Level. In process automation, there are two important standards
- Basic standard for functional safety: IEC 61508
- Sector standard for the application of functional safety in the process industry: IEC 61511
They set the standard for uniform and comparable assessment of devices and process engineering systems. The SIL level is determined by means of a risk assessment, for example by taking the following aspects into account:
- Possible extent of damage
- Length of time people spend in the danger zone
- Options for hazard control
- Likelihood of occurrence
Export this article
Download as PDFShare this article
Comments ({{comments.length}})
{{getCommentAuthor(comment, "Anonymous")}} {{comment.timestamp | date : "dd.MM.yyyy HH:mm" }}
{{comment.comment}}