Avoid blockages in cyclone vessels: Application of the month
The cyclone vessel is an important step in creating ingredients for cement. In this case, the ingredient is called clinker, which is made by sintering (heating and compressing) limestone and clay at elevated temperatures. These cyclone vessels are typically used in a series to preheat the materials before sending them to the rotary kiln.
The process begins with raw hot meal and hot gases being fed into one of these cyclone vessels. Due to their conical shape, the materials and the gases swirl inside like water flowing down a drain. The solids accumulate on the outside and most fall through the bottom opening to the next stage cyclone vessel. However, since these materials are accumulating on the sides of the vessel, too much buildup can cause a blockage and bigger problems at the plant. That’s why it’s important to measure the material and prevent a plugged chute.
The Challenge: A Hot, abrasive process
The Solution: Radiometric technology
Radiometric measurement solutions are completely external, and they come in two parts: a source with a low-intensity isotope and a detector. The source is mounted on the outside of the vessel and the detector is mounted opposite the source. The gamma energy from the isotope is directed toward the detector, and the detector “counts” the amount of energy reaching it. As more buildup occurs, the counts drop, signaling to the operator the vessel is getting closer to a total blockage.
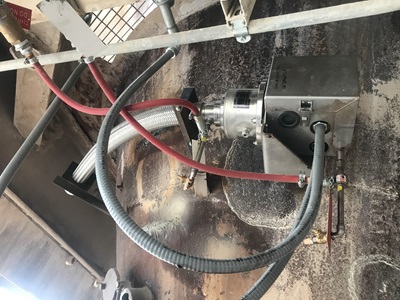
A cement plant in Texas uses a VEGA FiberTrac 31 for this measurement. The FiberTrac 31 is flexible, so it’s capable of wrapping around the conical bottom of this vessel and giving operators a broader view of any buildup. The entire setup mounts externally, avoiding any abrasive materials on the inside, and because this process operates at such high temperatures, VEGA representatives recommended an air cooling system to protect the internal electronics.
No more blockages
Learn more about this solution:
Contact the radiometric experts at VEGA and improve your process today.
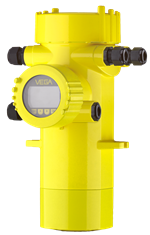
{{contact.DisplayName}}
{{contact.StakeHolderType}}
{{contactSearchMessage}}
Export this article
Download as PDFShare this article
Comments ({{comments.length}})
{{getCommentAuthor(comment, "Anonymous")}} {{comment.timestamp | date : "dd.MM.yyyy HH:mm" }}
{{comment.comment}}