Achieving on-time delivery for well pad assembly with VEGABAR 83
An instrumentation engineering and electrical services company in Louisiana builds well pad skids and engineers solutions for the upstream oil and gas industry. With a global reach, they cover hundreds if not thousands of well pads around the world. And, with versatility, time-consciousness, experience, imagination, and decades of industry experience, this company has a reputation to uphold. As sensor supplier lead time and supply chain issues started to pile up, the company started to worry if they could consistently get what they needed when they needed it.
What happens when you can't get your sensors on time?
The oil and gas industry is capital-intensive, and production delays increase operational costs and reduce revenue. Accurate pressure sensors are crucial for well control systems, and without them, critical monitoring and safety functions cannot be completed. Professionals in this sector can’t afford delays, and this engineering firm had to resort to expedited shipping to keep projects on schedule. This, in turn, drove up overall project cost.
The clock's ticking: time to find a better option
The company reached out to VEGA to discuss their sensor acquisition problems. Since each well pad has specific requirements, the VEGA team offered the VEGABAR 83 as the proper pressure sensor for their application. VEGA’s lead times outpaced their previous supplier, and on-time delivery ensured that the company got their sensors precisely when they needed them.
With safety as a constant concern, testing is of the utmost importance, and with Bluetooth connectivity, troubleshooting could be performed quickly and effectively without getting close to the assembly itself.
The VEGA Difference for this well pad integrator
Fast lead times, combined with reliable sensors and the right accessories delivered on time with no shipping snafus gave this integrator an immediate ROI. The VEGABAR 83’s accurate measurements, up to 0.075%, reflect the integrator’s commitment to building it right the first time. For extra peace of mind, plant professionals have access to myVEGA, a free online tool that gives information about prices and delivery time. And, if they have any questions or want to speak with a professional, VEGA’s support team is always available 24/7.
For instrumentation companies to succeed, they have to specify, assemble, and deliver quality products on time to customers around the world. They can't afford delays, so partnering with suppliers who ensure on-time shipments and provide high-quality sensors and accessories removes one concern for this engineering firm. That's why they chose the VEGABAR 83 for their well pad assembly needs.
Related industries
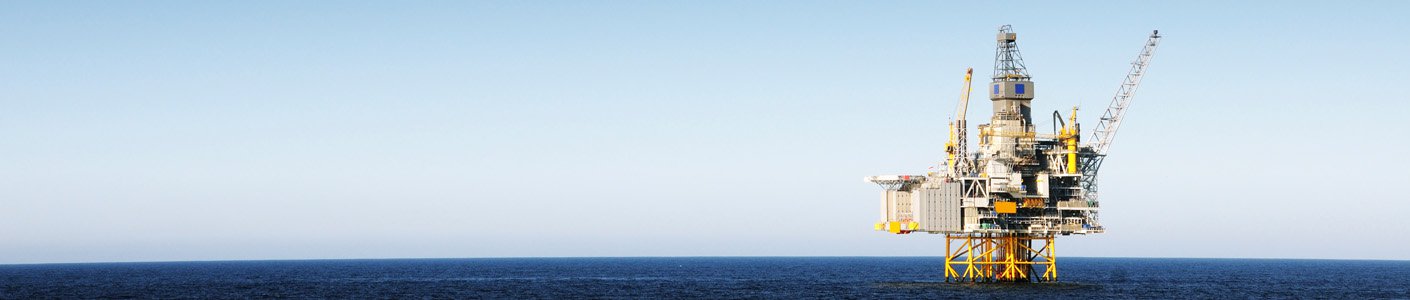
Oil and gas offshore
Related products
FAQs
The PIN for a Bluetooth PLICSCOM must be entered manually into a sensor before it can be accessed with the VEGA tools app.
Any VEGA sensor made since 2002 can be adjusted wirelessly up to 80 feet away using a Bluetooth PLICSCOM. This makes setup easier and safer when sensors are in hard-to-reach places or in locations requiring additional safety equipment.
A Bluetooth PIN is stored in the sensor, not in the PLICSCOM. Therefore, your PIN remains unchanged when you swap out the PLICSCOM.
When does it make sense to have a backup for your backup? When you are connecting multiple instruments to a controller, make sure to save a PACTware project during setup. If you lose your backup or have an issue with a device, you will be able to pull your configuration files to get back up and running in no time.
If you have several different VEGA sensors in a single area, you can pull all of them into a VEGASCAN 693 using an RS-232 or Ethernet connection. This can save on the amount of wiring while giving you a remote display and a single spot to configure all your instruments.
With the cable versions of our VEGAFLEX 80 series guided wave radars, make sure the cable is fully extended and taut. Slack in the cable can cause false signals and a measurement error.
When installing a cable version VEGAFLEX 81 guided wave radar on a mounting nozzle, make sure the rigid section of the probe is equal to or greater than the length of the nozzle. This is required for an effective false signal suppression, and it prevents the sensor from accidentally contacting the nozzle and giving a false measurement.
When you’re mounting a threaded version of a VEGAFLEX guided wave radar on a nonmetallic vessel, don’t forget to install a metal launch plate. This plate directs all the energy down the probe, prevents signal loss on the beam’s return, and it reduces the signal-to-noise ratio. Instructions for sizing and making the plate are in the manual.
When mounting point level switches like the VEGASWING on the side of a vessel, the forks should be parallel to product movement to reduce resistance to possible product flow. When measuring adhesive and viscous products, the forks should be vertical to reduce buildup. You can check the position of the tuning fork using the marking on the hexagon when installing it.
During installation, take an image of your application. That way, if a problem arises in the future you have an easy way to give our field service team a visual without being on-site. As they say, a picture is worth a thousand words.
When installing your VEGA device, be aware of your surroundings. Mounting instrumentation next to a heat source near or above the ambient temperature limitations can cause immediate damage or greatly reduce the lifespan of the electronic components.
During a radar setup, manual edits can be used to enhance the false signal suppression. However, manual edits do not replace the false signal suppression.
The four golden rules for a successful radar setup are:
1) Installation
2) Application
3) Adjustments
4) False Signal Suppression
Radar level measurement accuracy fully depends on providing the correct vessel measurements. Distance A and B set the 4…20 mA output, and these should be the exact distance from the radar reference point to the 0% and 100% points.
A reliable radar measurement starts with a successful installation. When you are installing your radar, be sure to consult your manual and pay attention to detail. Making sure the installation and wiring are done correctly from the beginning makes for a trustworthy radar you can count on.
All VEGAPULS radar units with an encapsulated antenna are shipped with a yellow protective cap. You must remove the cap prior to installation for proper level measurement. That radar signal can’t read through the protective cap if left on.
When you first open a VEGA ProTrac device from storage, make sure you reset the date and time through PACTware. This is a quick fix for error code F114 and ensures startup goes smoothly.
A radiometric continuous level linearization table requires a point for the maximum process value. Without this data point, the sensor will output an F066 error message. If you can’t fill all the way to the maximum process value, you can close the shutter(s) on the source(s) to represent full. Consult your source sizing sheet before doing so to make sure it is close to a 100% delta change application.
If you check the power of your ProTrac device with a multi-meter, but the detector still isn’t powering up, don’t assume the detector is bad. We use spring-loaded terminals, and sometimes the wire gets pushed in too far. Instead of clamping down on the copper wiring, it clamps down on the insulation. Once the wire is backed out, and the copper is secured under the spring terminal, power the unit back on to see if the detector comes to life.
With all of today’s technology, VEGA Field Service can support you remotely just as well as we can in the office. Please consider using TeamViewer on our website to let us assist you with your setup/troubleshooting needs in PACTware. Email a photo of the setup to service@vega.com to help us get a visual idea of how the equipment is installed and what the vessel looks like. If all you have is a PLICSCOM, we can even use Facetime to help.
Did you know you have field service experts at your fingertips with a click of a button? Downloading TeamViewer from VEGA.com allows users to give a secure ID number and password to a VEGA field service agent who can then see and navigate the user’s screen to troubleshoot a problem.
If PACTware is unavailable, and you’re connecting to a sensor with the VEGA Tools App, VEGA field service experts can provide remote support using the TeamViewer Quick Support App. This will allow a field service expert to view your phone and guide you through the troubleshooting process.
Export this article
Download as PDFShare this article
Comments ({{comments.length}})
{{getCommentAuthor(comment, "Anonymous")}} {{comment.timestamp | date : "dd.MM.yyyy HH:mm" }}
{{comment.comment}}