Taking the guesswork out of flow rates with VEGADIF 85
An Illinois-based municipal water treatment plant is responsible for treating the wastewater for over 28,000 residents. The wastewater facility is designed to handle an average flow of 16 million gallons of water per day, with a maximum flow rate of 24 million gallons per day and is permitted to discharge effluent as issued by the state’s EPA.
With strict environmental regulations around the concentrations of nutrients and solids in their wastewater discharge and locals counting on effective wastewater processing, knowing the plant’s flow rate is a key component for success. After this plant’s previous instruments became unresponsive, plant operators were left to guess their flow rate.
What happens when your sensors stop working?
The sanitary district runs its entire plant based on the flow readings from pumps that flow through pipes that send wastewater from holding tanks into their treatment process. A competitor’s devices, while initially fully operational, had suddenly become unresponsive. Without technical support or an immediate replacement available, plant operators had to play guessing games every day as to how much water was actually flowing through their system.
Accurate flow measurement is vital to keep operations running smoothly in any wastewater facility. Guessing the flow rate can compromise efficiency and jeopardize wastewater treatment across multiple stages of the process, including chemical dosing, aeration, filtration, and sludge management. Without these measurements, they’d run the risk of noncompliance with the EPA, reduce energy efficiency, and increase safety hazards.
Expanding our previous relationship
Plant operators were familiar with the quality of VEGA sensors, having previously installed radar units for level and overflow protection on their digester treatment vessels. They remembered how easy the sensors were to set up, monitor, and how effective they were at keeping their processes working efficiently. VEGA representatives met with plant personnel, and a solution was quickly developed. Five sets of the VEGADIF 85 differential pressure transmitter with VEGAMET 842 controllers were initially purchased and installed to control their plant flow.
Plant personnel continue to be impressed with the VEGADIF 85’s integrated overload diaphragm, a feature that gives them peace of mind with high reliability compared to their previous installation. Operators no longer need to guess how much wastewater is flowing through their facility, and with Bluetooth connectivity and the VEGA Tools app, setup, commissioning, and troubleshooting can be done with ease. As an added bonus, operators have 24/7 access to the VEGA field service team for outsourced expertise and a personal touch for any issues they might experience.
The VEGA Difference for sludge/screw press pressure measurements
After installing the VEGADIF 85 and VEGAMET 842 controller units, the Illinois-based wastewater facility has seen immediate cost savings. Knowing and controlling plant flow and processes eliminates unnecessary guesswork, allowing for predictable costs associated with energy consumption, chemical usage, aeration, and sludge treatment. Plant operators can rest easy knowing their facility is a safer place to work and compliant with EPA regulations, thanks to reliable and accurate measurements. In the long run, this plant trusts VEGA sensors so much that they’ve standardized their processes with VEGA instruments.
Wastewater plants can’t afford to guess flow rates when they’ve got safety, the environment, their employees, and the city’s residents at stake. That’s why municipalities need differential pressure sensors they can rely on. That’s why this plant chose the VEGADIF 85 and VEGAMET 842.
Related industries
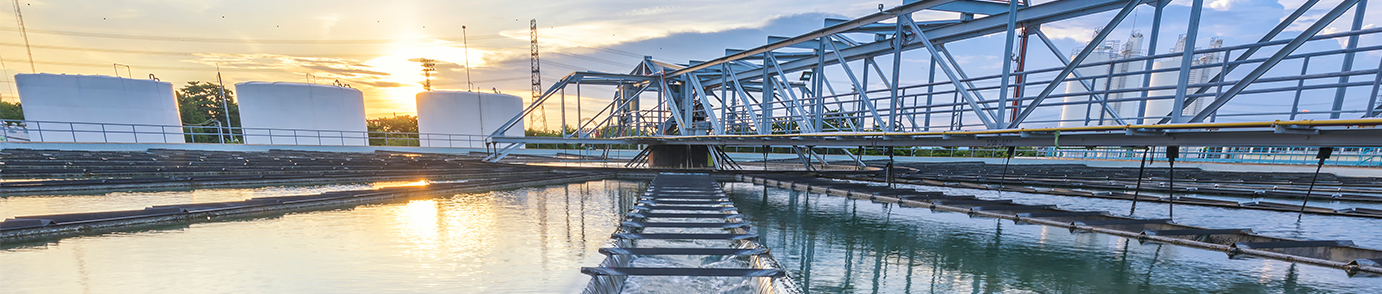
Wastewater treatment
Related applications
Sludge storage tank
Level measurement in the sludge storage tank
The digested sewage sludge is pumped into a sludge storage tank. This tank serves as an intermediate storage facility before the sludge is fed to the centrifuge or pressed for mechanical dewatering. To ensure optimal feeding, the sludge volume is monitored by a level measuring instrument.
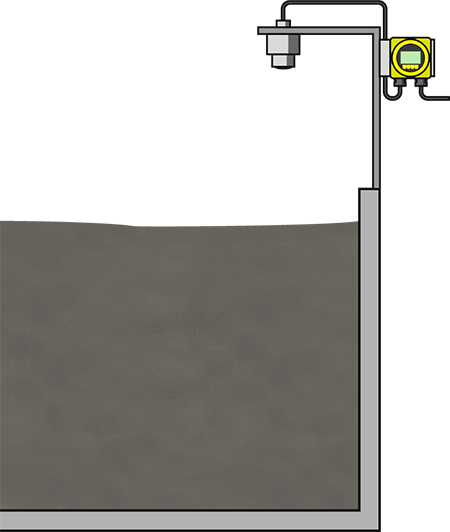
Reliable
Reliable content measurement in the sludge storage tank
Cost effective
Non-contact measurement ensures maintenance-free operation
User friendly
Simple installation and setup
Sludge receiving station
Sludge receiving station Level measurement
Sewage sludge from small decentralized sewage treatment plants or sewer cleaning operations is delivered in special vehicles. It is collected in a receiving tank and then gradually fed into the main sewage treatment plant for processing. Continuous level measurement determines the content of the receiving tank and controls the input to the plant.
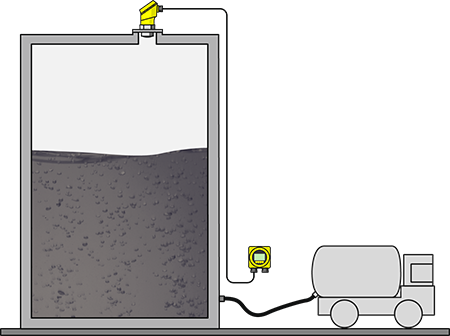
Reliable
Reliable content measurement under all operating conditions
Cost effective
Simple installation in existing facilities
User friendly
Maintenance-free operation even when heavily soiled
Related products
Export this article
Download as PDFShare this article
Comments ({{comments.length}})
{{getCommentAuthor(comment, "Anonymous")}} {{comment.timestamp | date : "dd.MM.yyyy HH:mm" }}
{{comment.comment}}