When wind and weather no longer matter, thanks to 80 GHz radar level sensors
The previous level monitoring systems delivered inaccurate readings due to weather, condensate and buildup
To produce fertiliser, the crude salt is mined underground, pulverised and then dissolved in water. The unusable components are then separated by means of flotation. In this process, huge quantities of the caustic solution are pumped back and forth to achieve a higher brine concentration. Two so-called 'Intze' tanks, which are 15 meters high and particularly noticeable due to their shape and design, serve as buffers for the liquid.
The two storage tanks require continuous level measurement to ensure that the level is monitored at all times: On one hand for environmental and operational safety reasons, and on the other, to enable precise calculation of the buffer capacity. Because brine is extremely aggressive, non-contact level measurement has always been the preferred method. But due to the conical shape of the tanks, the deepest measuring point is located in the interior, far from the outer edge. The initial solution was to construct a very long boom, with a level gauge mounted at the end, so that measurement could be carried out exactly in the middle of the tank. Another challenge was the heavy buildup of deposits on the tank wall.
Storage and buffer tanks
Level measurement and point level detection in small storage and buffer tanks
Storage and buffer tanks enable a reliable material supply for various ongoing processes. The plant operators need to have exact level data from these tanks at all times to ensure timely replenishment and facilitate continuous production. In addition, the measured values form the basis of the statistical consumption analysis for validation and quality monitoring.
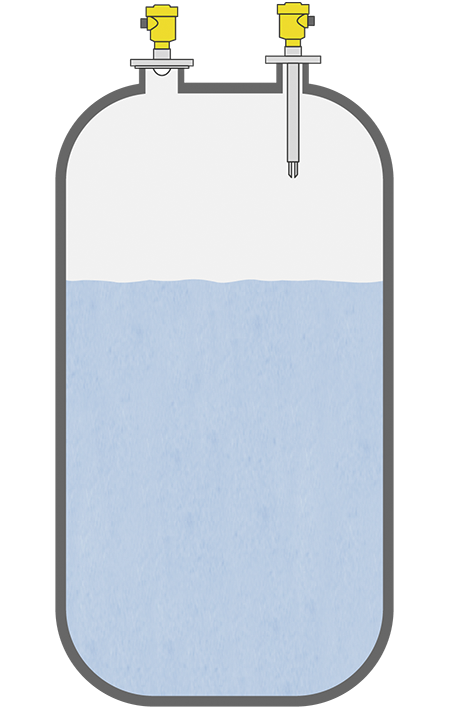
Reliable
Reliable protection against overfilling
Cost effective
Independent of product and process characteristics
User friendly
Simple to set up with maintenance-free operation
At first, the engineering team tried a measuring method based on ultrasound. However, the large measuring distance led to incorrect measurements, and condensation from rain or snow also caused difficulties. Later, a radar level transmitter was installed and used for many years. This 26-GHz instrument with horn antenna actually provided correct readings, but strong gusts of wind or snow put a lot of strain on the boom.
VEGAPULS 64 optimises level measurement with 80-GHz technology
This allowed the boom to be shortened. The measuring instrument from VEGA was mounted slightly tilted and yet was still able to detect any filling level accurately.
The high dynamics now made it possible to use a considerably shorter boom, as the sensor could be mounted at a slight angle to the surface of the liquid. This is not usually recommended when measuring flat liquid surfaces, because a large part of the transmitted energy is reflected off to the side, as with a mirror, and thus does not get back to the receiver. However, there was a slight wave movement on the surface, it was enough for a small part of the energy to be reflected back in the direction of the sensor to achieve a reliable measurement thanks to its large dynamic range. This meant that the wind load was reduced considerably due to being able to use a shorter boom.
Thanks to 80 GHz, reliable level measurement is possible at all times (even in snow and stormy weather) despite the difficult tank shape.
What is more, the deposits in the vessel have little effect on VEGAPULS 64. Here, too, the measurement benefits from VEGAPULS 64’s very narrow beam angle of 4°, which is a big contrast to the 10° beam angle of the previous 26-GHz radar sensor with DN 80 antenna. This allows the sensor to be used even in vessels with internal installations or heavy buildup on the walls, as the measuring beam simply passes by such obstacles.
K+S at the Zielitz site was one of the first to use the newly launched VEGAPULS 64. As their confidence in VEGA technology was already strong – K+S has been working with VEGA for over 25 years – the company decided that a test run with the new instrument wasn’t necessary. As expected, since the radar sensor installation, there have been no problems with condensation, gusting winds or snow.
Conclusion
Related products
Related industries

Applications
Export this article
Download as PDFShare this article
Comments ({{comments.length}})
{{getCommentAuthor(comment, "Anonymous")}} {{comment.timestamp | date : "dd.MM.yyyy HH:mm" }}
{{comment.comment}}