Continuous level measurement with level sensors
Continuous level measurement with level sensors
In a nutshell: Continuous level measurement
What methods are used for continuous level measurement?
The following measuring principles can be used for continuous level measurement:
- Level measurement with radar
- Level measurement with guided radar
- Level measurement with ultrasonic
- Capacitive level measurement
- Hydrostatic level measurement
- Radiometric level measurement
Which measuring principle is the right one depends on where the level transmitter is to be used. We’re happy to assist you in finding the right level sensor for your application.
đŸ’¡ 5 important criteria for selecting the right level sensor
What are the advantages of VEGA level transmitters?
Where can level sensors be used?
Typical applications for continuous level measurement in the process industry are:
- Process tanks
- Storage tanks
- Silos
- Mobile containers
Level gauges are mostly used for good such as:
- Liquids
- Pastes and slurrys
- Powders, grains and granules
- Bulk solids
What requirements must level sensors meet?
The primary goal in the manufacturing and processing of products is consistent product quality. In order to achieve this, rigorous demands, which vary from industry to industry, are also placed on the measurement technology used.
VEGA has the right level sensor for every application:
- Exact measuring results independent of process conditions: even at high temperatures and pressures
- Reliable level control, even in the presence of foam and condensate thanks to non-contact measuring methods
- High mechanical stability for harsh ambient conditions
Level sensors from VEGA can also be used in these areas:
- Hazardous areas and safety-related systems up to SIL2
- Chemically aggressive media
- Hygienic applications in the food and pharmaceutical industries thanks to certified materials and process fittings
There are also suitable, cost-effective solutions for standard applications that place only low demands on temperature, pressure and chemical resistance.
Reliable level control for your industry
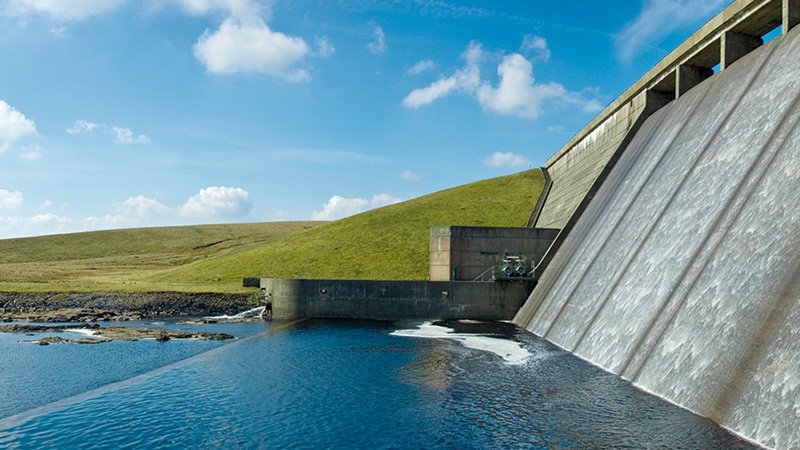
Water and wastewater
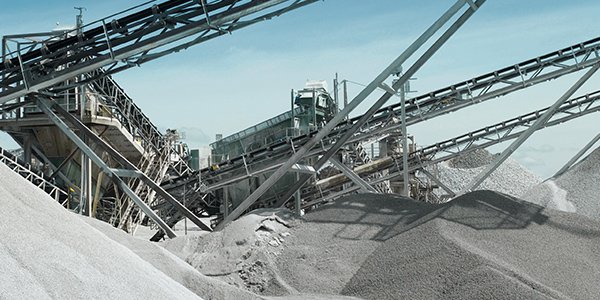
Building materials
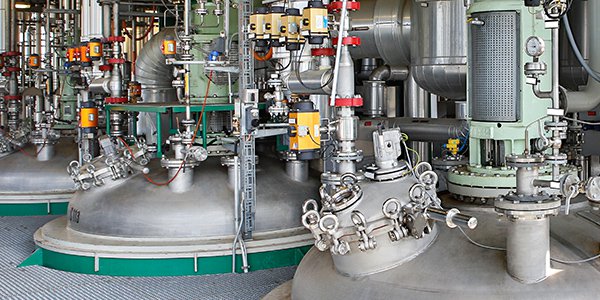
Chemical industry
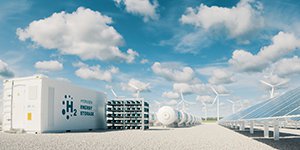
Energy
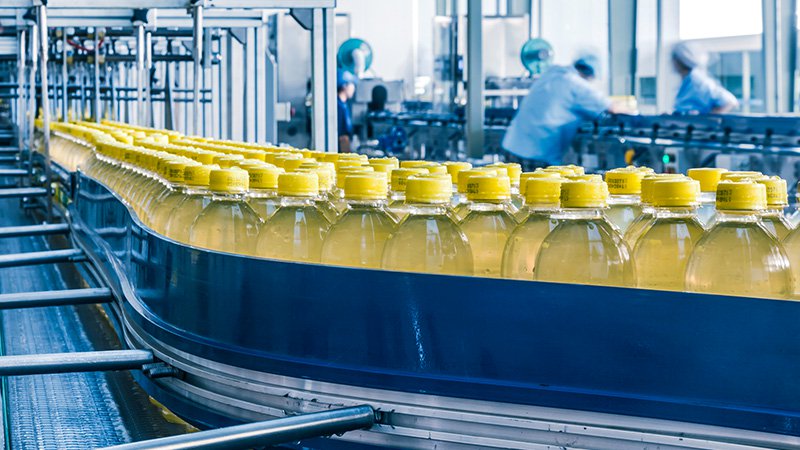
Food industry
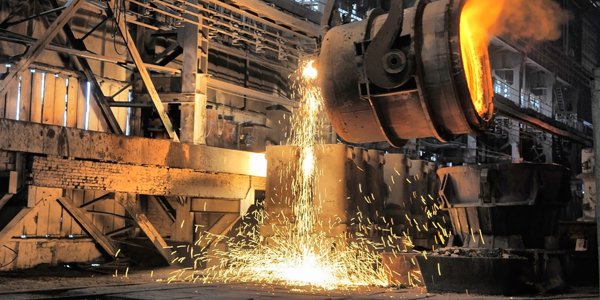
Mining and metal production
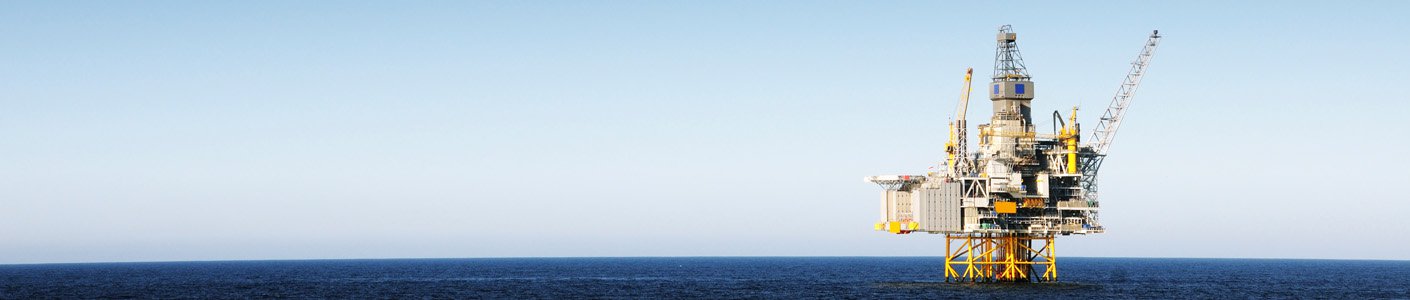
Oil and gas offshore
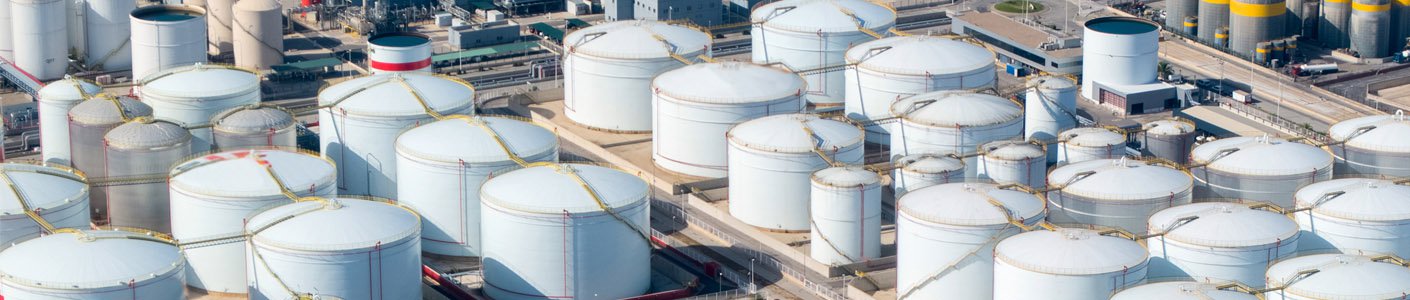
Refining and petrochemical

Pharmaceutical industry
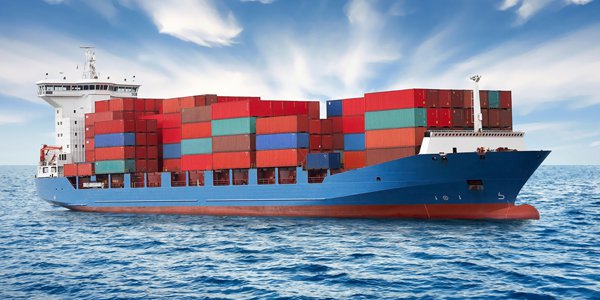
Ship and yacht building
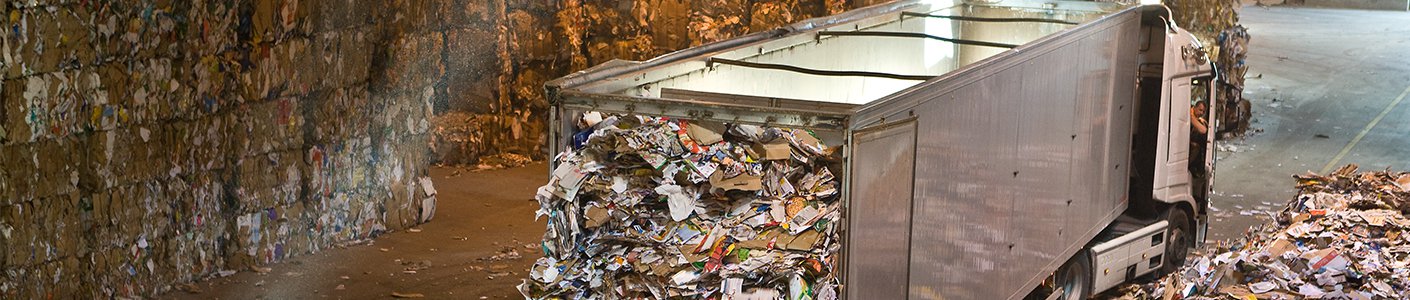
Environment and recycling
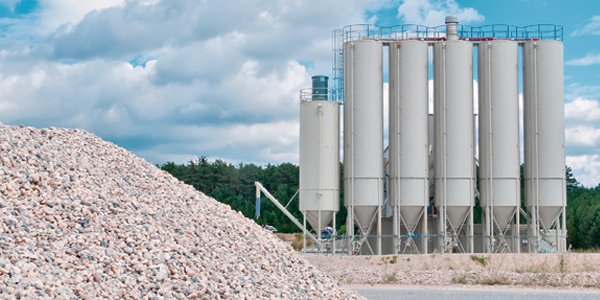
Cement
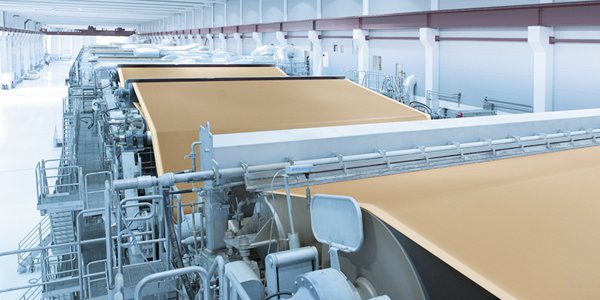
Close