Signal Conditioners: The Translational Heroes
Think of signal conditioners like your cable box: a digital signal comes from the cable company through a wire and into the cable box where that digital signal of ones and zeroes is turned into images and sounds in the form of a picture on your TV. Signal conditioners take jumbled information in an industrial process and make it understandable for the system as a whole. In other words, signal conditioners convert one type of electronic signal into another type of signal. This paper will explain the importance of signal conditioners, their many capabilities, and the technological progress that’s been made in the past 20 years.
A long journey
The incremental leaps of technology in the world of digital and computer electronics have allowed signal conditioners to perform at new levels not experienced in the past. There are various types of signal conditioners, and each serves a purpose, ranging from a simple display to intelligent units controlling pumps, valves, or motors. There are units that process sensor data from multiple instruments and send the data via wireless transmission, Ethernet, or other communication protocols to the cloud.
Seeing is believing
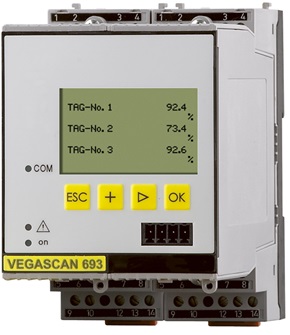
A setup like this one can save customers tens of thousands of dollars on installation and wiring costs. The ability to run smaller conduit and use less wire can help justify the ROI on new level measurement and inventory management capital projects. Additionally, this signal conditioner includes a built-in webpage to view the measured values and health status of the sensors in real-time. A built-in e-mail server allows the customer to program and send critical high and low level events, time-based reports with level measurement, and inventory information. In the event that something stops working correctly, there’s an added bonus of remote support and troubleshooting over the customer network, all the way down to the individual sensor. These are all features that allow operators to more efficiently manage their process.
Another set of “eyes”
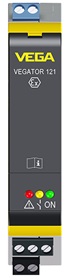
The VEGATOR 121 can be used in tandem with a high level switch for liquids, and not only can it ensure a proper level is maintained within the vessel, but the signal conditioner can also run a function test on the switch electronics, replacing an annual wet test to save time and money. Throughout the year, the signal conditioner can also monitor the switch for failure and monitor the wiring for open or short circuited conditions.
Making the unsafe safe
Some processes can be hazardous or explosive in nature, and regulations put restrictions on the amount and type of power to any instruments monitoring those processes. This is, once again, where signal conditioners come to the rescue. This type of signal conditioner can reliably separate intrinsically safe and non-intrinsically safe circuits.
VEGA’s VEGATRENN series of signal conditioners can provide an optimum supply of power to the connected sensors. These signal conditioners can take universal voltage sources (20-230Vac or 24-65Vdc) in the facility and translate it into a safe, low voltage electricity in the hazardous area that will not allow arcs or sparks.
Bluetooth bonus
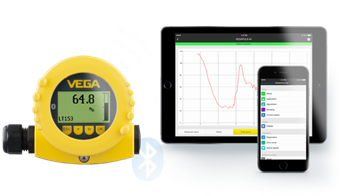
Instruments as far back as 2003 are even being brought into the present with VEGA’s new technology. The PLICSCOM with Bluetooth can retrofit onto older VEGA instruments, transporting them to the cloud and the world of IIoT. It can do all of this safely and securely as it’s armed with two shields of data security: a PIN that syncs an individual device with the VEGA Tools App and encryption software that keeps unapproved users from accessing data.
Conclusion
Related products
Export this article
Download as PDFShare this article
Comments ({{comments.length}})
{{getCommentAuthor(comment, "Anonymous")}} {{comment.timestamp | date : "dd.MM.yyyy HH:mm" }}
{{comment.comment}}