Revolutionary chemical manufacturer refines processes with VEGABAR 38
A chemical manufacturer in Houston, TX, uses a "first of its kind" technology to convert sustainable feedstocks into essential materials, without any harmful byproducts and minimal emissions. The state-of-the-art plant features twenty-two storage tanks, multiple poly tanks, oxidation reactors, carbon decolorization skids, and future projects involving five permeate tanks and another tank farm.
Cutting-edge technology requires sensors that can keep up with the latest innovations. With a traditional pressure sensor with a metallic diaphragm in place, this plant started to experience less than ideal processing conditions – not something you want in your industry-leading company.
Dextrose laboratory: chemistry at work
Dextrose, a form of glucose, is used as a feedstock in chemical reactions. Having accurate pressure measurement in the dextrose supply lines ensures that the material is delivered consistently at the right flow rate, avoiding fluctuations that could impact the reaction kinetics and product quality. When dextrose rises above a 50% concentration in the line, it hardens and crystallizes, leading to blockages.
When it happened in this facility, plant operators had to remove their pressure transmitter for cleaning before reinstalling it. With the previous sensor, the cleaning process was difficult at best, and made more complicated due to the sensor’s metallic measuring cell that could be easily damaged.
Halting processes, cleaning, reinstalling, and replacing sensors as they broke limited throughput, cut into revenue, and reduced energy efficiency. For this business to thrive and deliver ground-breaking results, their processes needed a second look.Maintenance-free process indication at a glance
After speaking with plant professionals and hearing their concerns about their current measurement solution, VEGA representatives offered an alternative: a VEGABAR 38 with a CERTEC ceramic measuring cell. The ceramic measuring cell provided durability and required minimal maintenance, standing up to the harshest process and cleaning conditions with ease.
Outside of the new measuring cell, operators loved how the sensor could be connected to via Bluetooth, making installation, startup and commissioning a breeze. With the sensor’s 360-degree light ring, operators were immediately able to determine the process status at a glance across the floor, which saved them time and increased plant safety.
After their first successful install and zero issues reported, the manufacturer placed orders for many more VEGABAR 38 sensors to be used in other applications across the facility.
The VEGA Difference for dextrose line pressure measurements
When your company is looking to change the way essential materials are manufactured, fine-tuning your processes across the organization is always a top priority. With the new VEGABAR 38 sensor installed, plant workers no longer need to take the device out of operation and worry about the cleaning process or damaging the measuring cell. It means one less item that requires maintenance during regular checks.
Challenging the status quo is never an easy task. It requires dedicated professionals and those willing to critically analyze existing systems for areas of improvement. This manufacturer made the right choice by switching to the VEGABAR 38. With a 360-degree light ring for process indication, Bluetooth connectivity, ease of setup and commissioning, a durable measuring cell, and technical support a click away, this company is well-equipped for the future. That’s why this plant chose the VEGABAR 38.Related industries

Applications
Related applications
Storage tank
Level measurement in storage tanks
In the production of pigments, aggressive raw materials such as chlorobenzene, hydrochloric acid and sodium hydroxide are used. They are stored in horizontal cylindrical tanks and filled through a dip pipe to reduce splashing and fume generation. A reliable level measurement ensures safe handling and continuous material availability for optimum productivity.
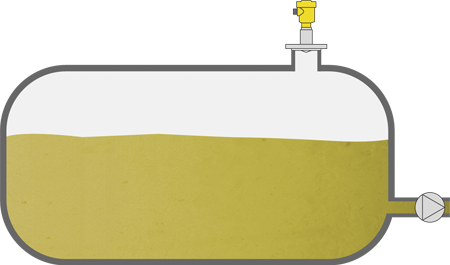
Reliable
High process reliability thanks to reliable measurement
Cost effective
Highly resistant materials enable long service life
User friendly
Simple installation and maintenance-free operation
Related products
Export this article
Download as PDFShare this article
Comments ({{comments.length}})
{{getCommentAuthor(comment, "Anonymous")}} {{comment.timestamp | date : "dd.MM.yyyy HH:mm" }}
{{comment.comment}}