Tecnica di misura di VEGA per l'ottimizzazione di frantumatori
La chiave consiste in un'automazione intelligente dell'intera catena del processo produttivo e nella gestione in tempo reale dei dati. I sistemi Ma-estro scompongono per così dire l'intero processo, dalla cava al prodotto finale, e valutano da vari punti di vista i singoli parametri nei relativi processi, consentendo in media una riduzione dei consumi energetici del 15%.
Processi ottimizzati per un buon prodotto finale
I sensori VEGA installati negli impianti di frantumazione rilevano l'esatto livello in qualsiasi momento.
La qualità e la riproducibilità dipendono a loro volta dal carico nelle macchine di frantumazione: più il materiale è duro e più vengono sovraccaricati frantoi e mulini. Anche l'umidità può diventare un problema per nastri trasportatori, idrocicloni e vagli. Inoltre le caratteristiche del materiale grezzo quali massa, densità e durezza, non sono uniformi, per cui i componenti dell’impianto come frantoi e vagli vengono sollecitati in modo variabile.
Il rilevamento affidabile del livello consente di evitare il sovraccarico
Il principale obiettivo del controllo automatico è l'individuazione e l'eliminazione degli squilibri causati dalla variabilità dei materiali lavorati.
Ma-estro impiegava già in precedenza sensori di altri costruttori per questi compiti, ma la loro integrazione nei sistemi di automazione esistenti era molto complessa. La polvere, i materiali residui e l'umidità causano una serie di riflessioni di disturbo che creavano grossi problemi ai sensori impiegati precedentemente, causando imprecisioni di misura.
Installati per un test e poi adottati definitivamente
Soprattutto il VEGAPULS 69 con i suoi valori di misura estremamente precisi offre le premesse necessarie per l’ottimizzazione dei processi. Il sensore di livello lavora con una frequenza di 80 GHz e un diametro dell'antenna di circa 75 mm. Grazie al ridotto angolo di apertura, il raggio a 80 GHz evita eventuali installazioni interne o adesioni sulle pareti dei serbatoi. Inoltre passa attraverso dense nuvole di polvere senza alcun problema. Questo rende la misura sicura e affidabile anche in ambienti difficili, come quelli degli impianti di frantumazione.
L'azienda italiana ha apprezzato molto anche la possibilità di impiegare una comunicazione wireless tramite Bluetooth. Questo è particolarmente interessante per punti di difficile accesso, ambienti industriali difficili e aree Ex. L’utente può effettuare la configurazione e la parametrizzazione dei propri sensori con lo smartphone o il tablet in tutta comodità e a distanza di sicurezza, disponendo anche di utili funzioni di visualizzazione e diagnosi. La tecnologia di VEGA si integra quindi perfettamente nella filosofia di ottimizzazione di Ma-estro.
Applicazioni
Grandi sili per lo stoccaggio
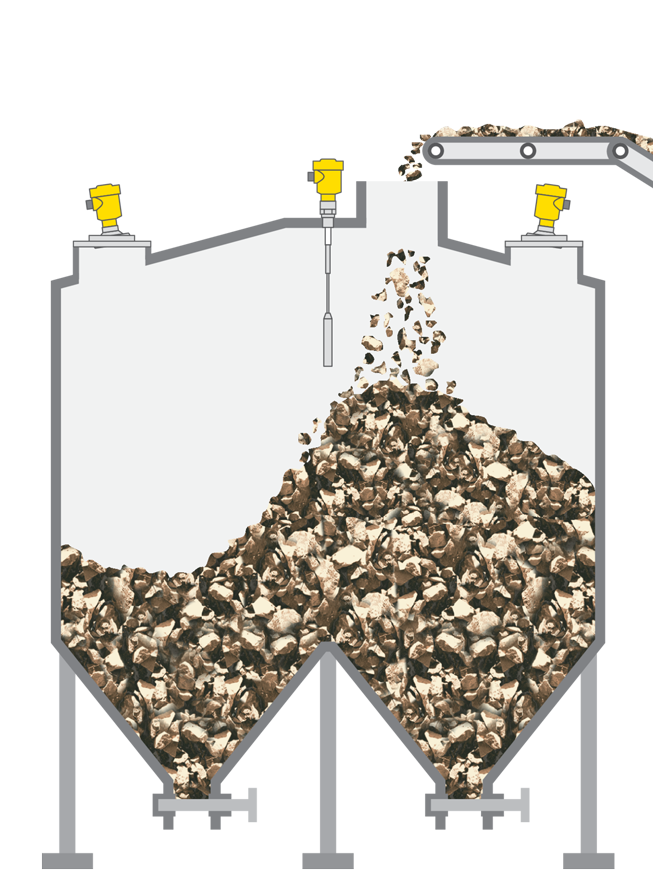
Misura di livello e rilevamento della soglia di livello nei grandi sili per lo stoccaggio
Alla sezione ApplicazioneCumulo di solidi in pezzatura
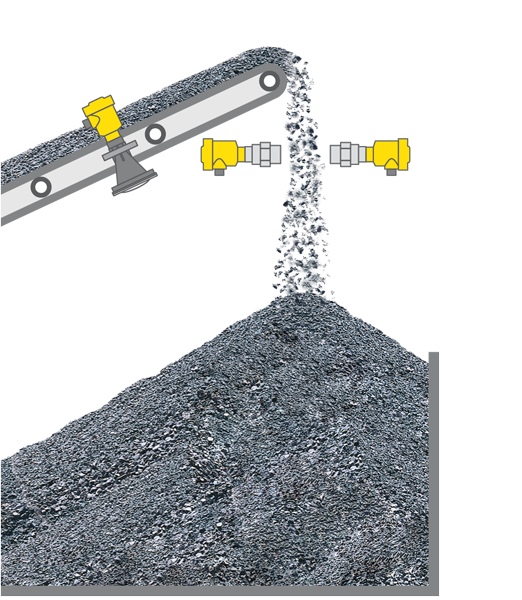
Misura di livello di materiale in cumuli
Alla sezione ApplicazioneFrantumatore
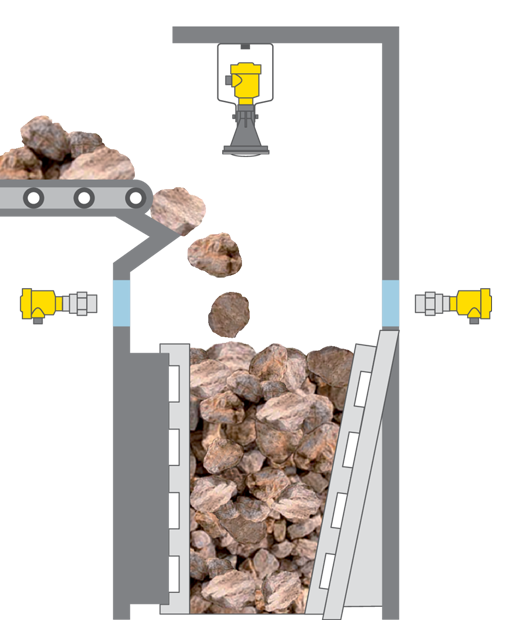
Misura di livello e rilevamento di soglia di livello nel frantumatore
Alla sezione ApplicazioneNastro trasportatore
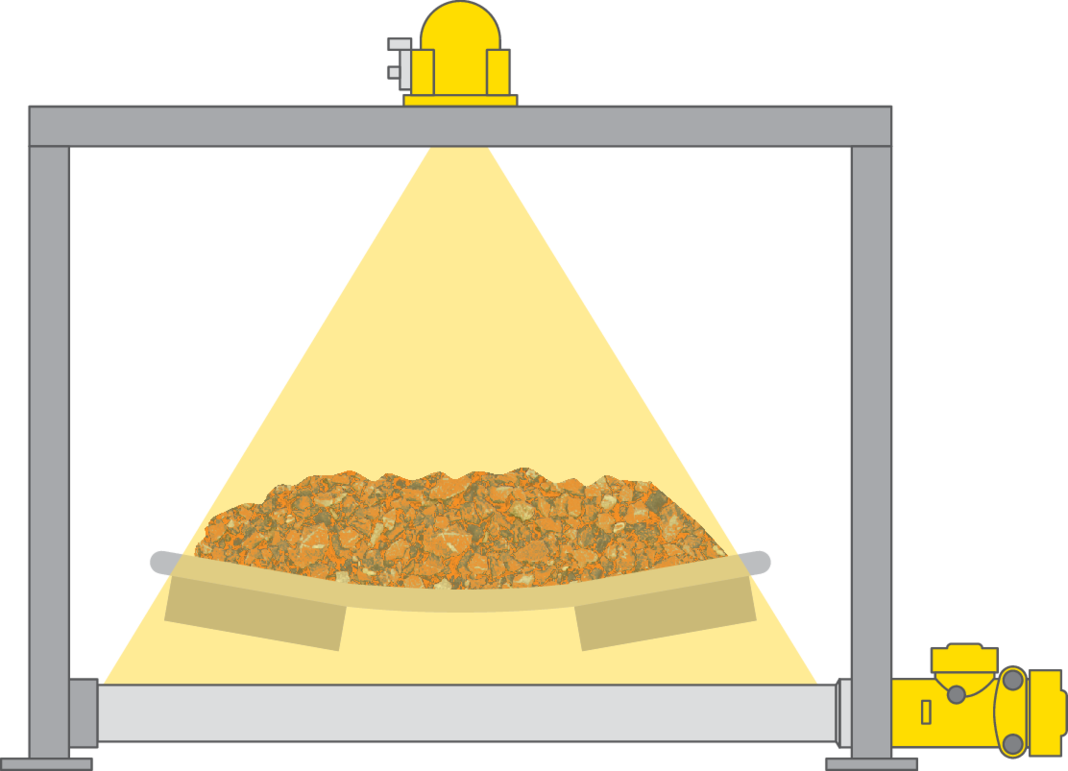
Rilevamento del flusso di massa sul nastro trasportatore
Alla sezione ApplicazioneProdotti
We need your consent
This content is provided by an external provider. If you activate the content, personal data may be processed and cookies set.
Esportazione di questo articolo
Scarica come PDFCondividi questo articolo
Commenti ({{comments.length}})
{{getCommentAuthor(comment, "Anonimo")}} {{comment.timestamp | date : "dd.MM.yyyy HH:mm" }}
{{comment.comment}}